Let's Talk About Quality Assurance In Commercial Warehousing
Wed, Jul 19, 2023
By: Jacob Gilmore
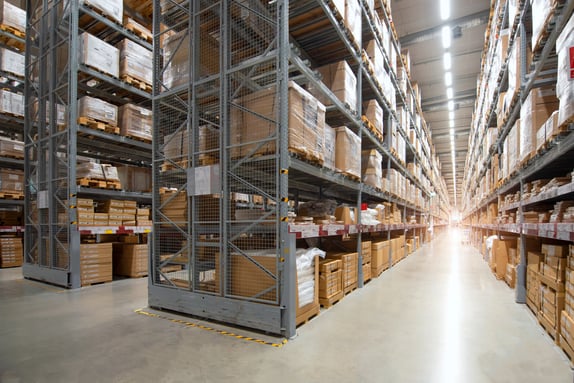
Commercial warehouses use two methods of quality monitoring their operations: Quality control and quality assurance. Many warehouses use the terms interchangeably, but there is a difference. Your main office could be hundreds or thousands of miles from a commercial warehouse, depending on your operations. You’re not there to make sure the commercial warehouse is doing its job. Gilmore provides quality assurance for all warehouse transactions to ensure that your product is handled and delivered with care.
What is Quality Assurance?
Warehouse quality assurance monitors and evaluates the quality of your warehouse, including its operations. Your business sets standards, and our quality assurance team ensures the warehouse meets those standards.
We ensure that your products are received by us and sent out safely, timely, and consistently. We check the condition of shipments prior to them leaving the warehouse to ensure your customers receive only quality goods.
With quality assurance procedures, you can identify defective items earlier in the supply chain – before they reach your customers. That way, your brand reputation stays intact.
Quality assurance and quality control not only improve warehouse efficiency but can help reduce errors and save money.
Quality Assurance vs. Quality Control
While quality assurance and quality control measure the effectiveness of your warehouse processes, quality control measures it in batches. Quality assurance measures the effectiveness of your warehouse processes for individual products.
For example, with quality control, inspectors would inspect a batch of products instead of individual products. Without quality assurance, which is an essential part of your business, you could lose money, time, and customer trust that you worked so hard to build.
Quality Control Procedures
Our quality assurance workers have a step-by-step list or guide on how your warehouse operations should work. They include how employees work with machines and materials, information about the types of tools and supplies they need to complete their tasks, and more.
We ensure we keep the documents outlining your standards up to date so we are always within your standards and can work efficiently. Should something go wrong with a customer order, we can look back through the documentation to determine the problem.
Part of the process for quality assurance includes:
- Pallet Inspection: Workers look for broken boards, unevenness, moisture damage and delamination. If a pallet has damage, workers report it to their managers.
- Individual Item Checks: Employees check each item on the pallets for defects and remove the item from the pallet if any are found. We send it back to be corrected.
- Labeling: Incorrect labels cause customers to receive the wrong order and cause inventory errors, which also affect manufacturing and more. Employees ensure all boxes have the proper labels, including content descriptions and SKU numbers. If an item is returned later, then you know where the item was shipped from.
Quality assurance can be handled manually or with automated software. At Gilmore, we use automated software to ensure everything is correct, including cross-dock solutions, packing services, pick-up services, white-glove receiving, inventory control, white-glove deliveries, and tailgate deliveries.
Contact Gilmore
Keep your business property safe and secure with our warehouse services. Our warehouse is climate-controlled and can protect against flooding, hurricanes, and more. For more information about commercial warehousing and our quality assurance procedures, contact Gilmore today.